How New Tariffs Are Impacting UK Contractors
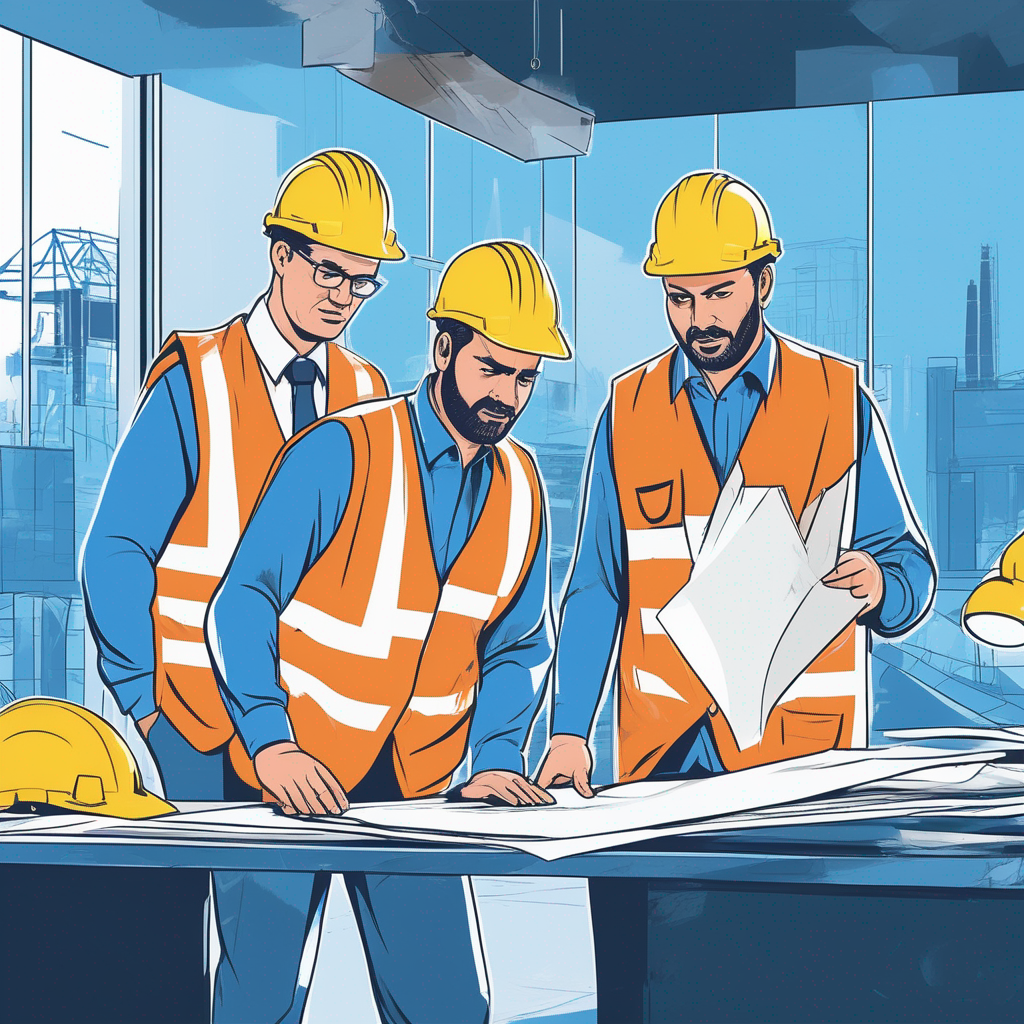
Facing Rising Costs Due to Tariffs
Recent changes in global trade policies, especially the introduction of new tariffs on imports from China, have quickly become a pressing issue for UK contractors. These tariffs are driving up the costs of essential building materials – from steel and aluminium to finished fixtures. This is more than just a headline; it’s a daily concern for those quoting on new jobs or managing existing projects.Take, for example, a medium-sized contracting business in Manchester. Previously, they could estimate the cost of imported steel fairly accurately, but tariff changes now mean that the price in January might look very different from March. That level of unpredictability throws a wrench in the works for project planning.
How Price Volatility Complicates Project Management
The knock-on effects of these tariffs are being felt in several important ways:- Material Costs Are Increasing: The tariffs add additional import fees, and suppliers are often passing these higher costs directly onto contractors in the UK.
- Unpredictable Pricing: Prices are fluctuating rapidly, making it difficult to lock in costs ahead of time. This complicates budgeting and financial planning for both current and future projects.
- Estimating Is Tougher: Contractors are finding it more challenging to provide accurate quotes to clients, which increases business risk and could impact relationships with customers.
- Review supplier agreements regularly to ensure you’re protected from sudden price hikes.
- Build contingency funds into project budgets to absorb unexpected costs.
- Communicate proactively with clients about price risks and possible changes.
- Explore alternative suppliers outside affected market zones if feasible.
"We used to be able to give customers a quote with confidence. Now, every tender feels like a gamble," says a London-based construction manager.
Consider this: A contractor estimates a £10,000 cost for imported materials pre-tariff. Overnight, a 15% tariff bumps that by £1,500. The thin margins in construction mean absorbing these costs is rarely an option.
Project Delays and Cancellations Are on the Rise
Increased materials costs and price swings affect more than just the bottom line. Many contractors are facing tough choices:1. Delay start dates to renegotiate supply contracts. 2. Pause work until prices stabilise. 3. Cancel projects that no longer make financial sense after cost adjustments.
A recent survey by a UK contractors’ association revealed that nearly 40% of firms have delayed projects in the past year due to supply-side volatility.
What Contractors Can Do Next
While tariff changes may be out of your control, there are steps you can take to minimise their impact:Risk Factor | Impact | Mitigation |
---|---|---|
Increased Material Costs | Reduced margins | Renegotiate supplier deals |
Price Volatility | Difficult estimation | Fixed-price contracts |
Project Delays | Client dissatisfaction | Regular progress updates |
Stay Ahead in a Changing Landscape
If you’re a contractor in the UK, staying informed about global policy changes is more vital than ever. Navigating the complexities of material sourcing, estimating, and project management in this climate can be challenging – but not impossible.Keep your team and your clients in the loop, and seek expert advice when needed. The construction sector has weathered storms before, and with smart planning, it can handle this one too.
Ready to future-proof your business? Start by reviewing your current project bids and suppliers to build in flexibility and resilience for the months ahead.